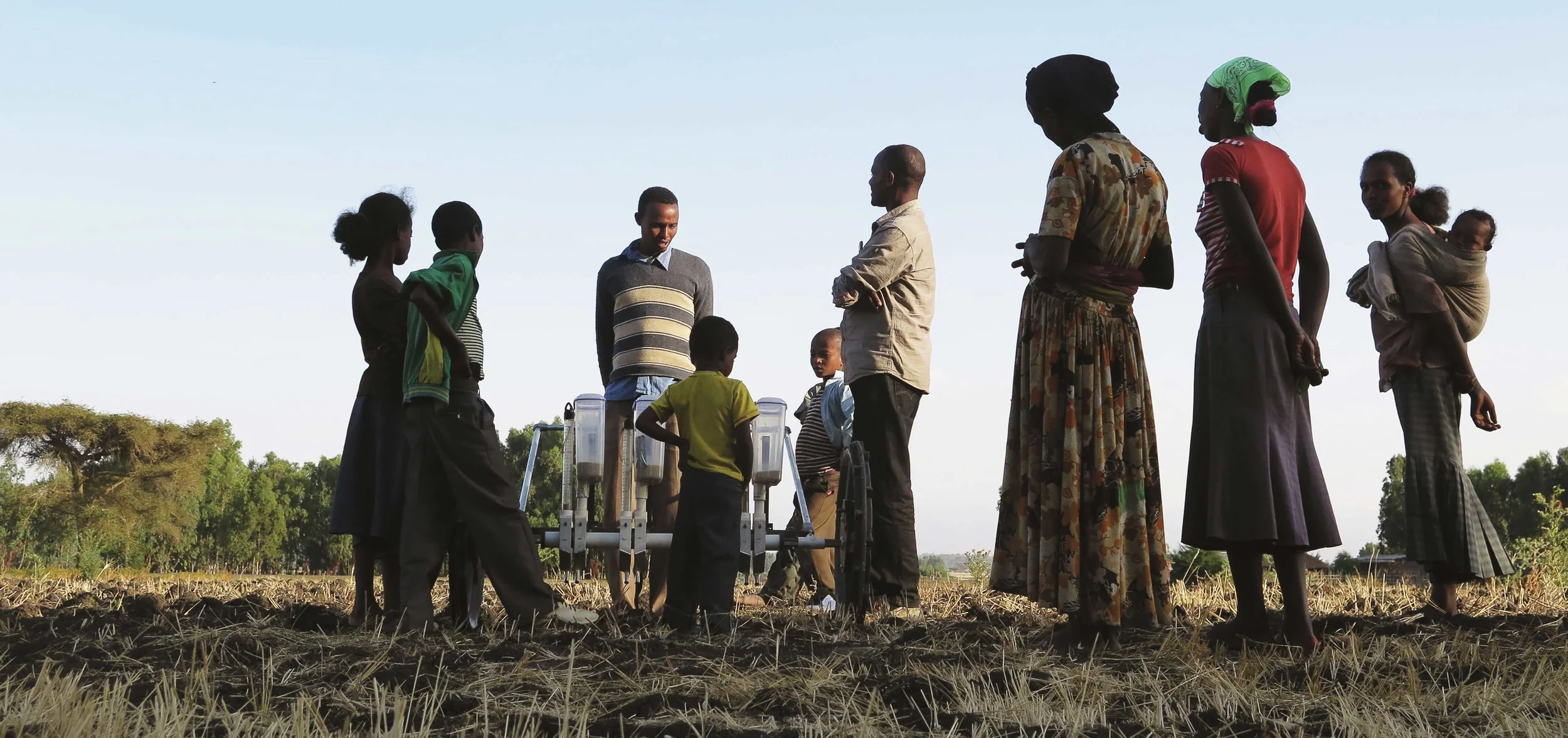
IDEO - Teff Row Planter
A joint effort between IDEO.org and the Agricultural Transformation Agency (ATA) in Ethiopia, with funding from the Bill and Melinda Gates Foundation. The goal was to create an inexpensive, locally produced row planting tool to help Ethiopian farmers increase their crop yields and stimulate economic development.
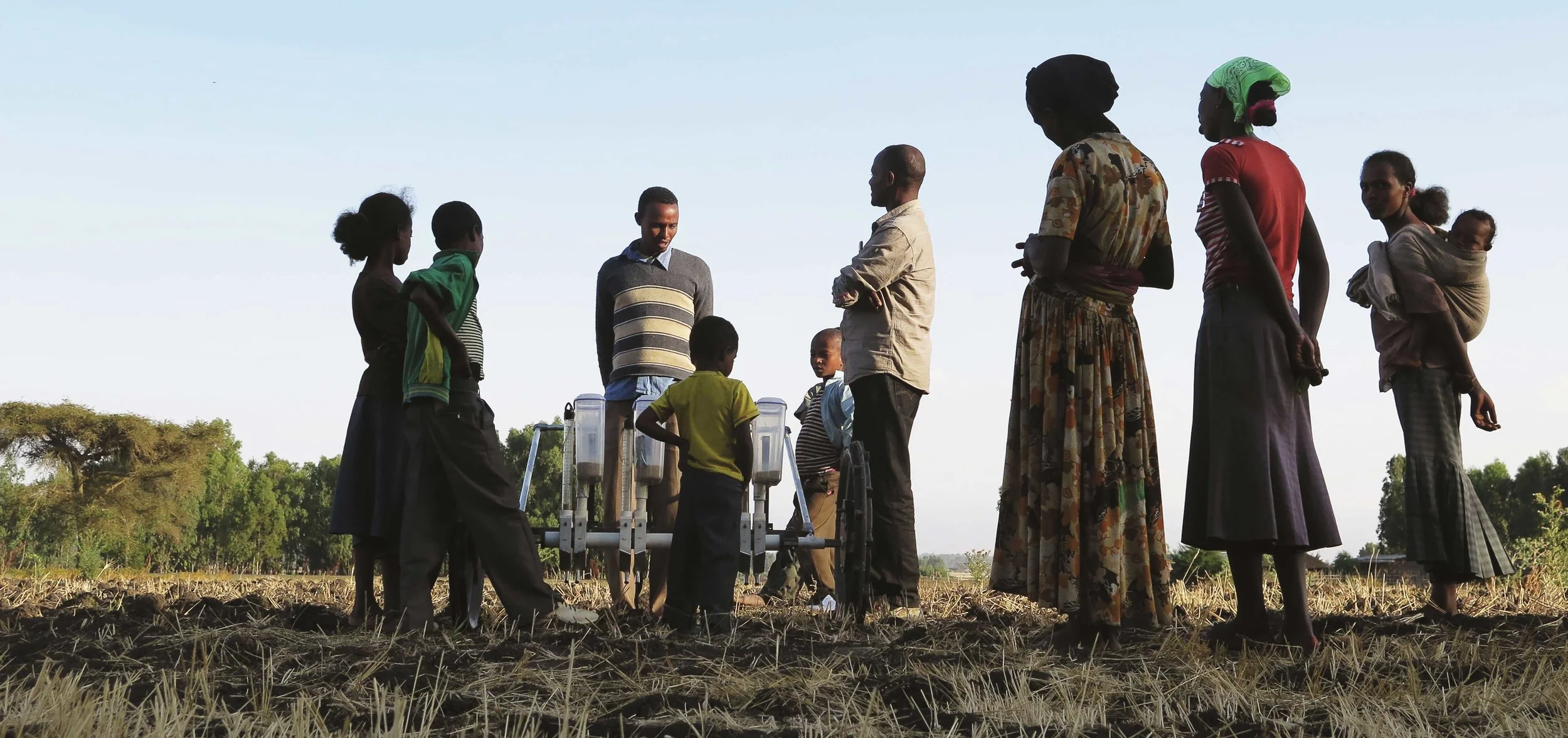
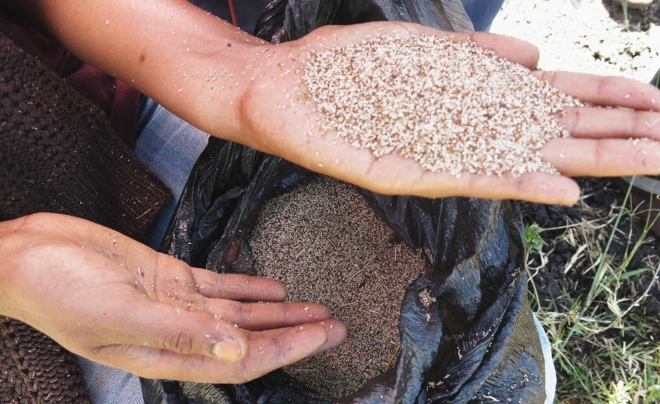
Teff is a non-glutenous grain that is used to make Injera, a sort of thin, fermented, sourdough pancake that is the staple food of Ethiopia. Because Ethiopia does not produce enough teff internally to satisfy the needs of its population, they are barred from exporting it. Most of the farming in the country is done by rural subsistence farmers tending their small plots of land in the same way they’ve done for thousands of years. We were seeking to create a tool that would leverage modern farming techniques, like row planting and side by side fertilizing, in a package that was affordable for the farmers to purchase, human-powered, and simple enough for them to fix on their own.
The first challenge was to design a method for dispensing seeds with regards to ensuring that seeds were dispensed in the correct quantities and evenly spaced. We didn’t re-invent the wheel, but instead modified existing seed wheels from similar planters to work with the tiny grains and the non-uniform fertilizer size. The result was a side by side seed and fertilizer dispenser. The one shown here was the third iteration made from simple injection molded plastic pieces, a few springs to maintain contact between the metering wheels and the control pads, and an O-ring to hold everything closed.
During the design process we also had to account for the fact that the planting season for teff in Ethiopia is the wet season. That meant that humidity was an issue and we needed to ensure that our seed metering device would continue to work if and when it got wet. We created a simple humidity chamber to simulate worst case planting conditions.
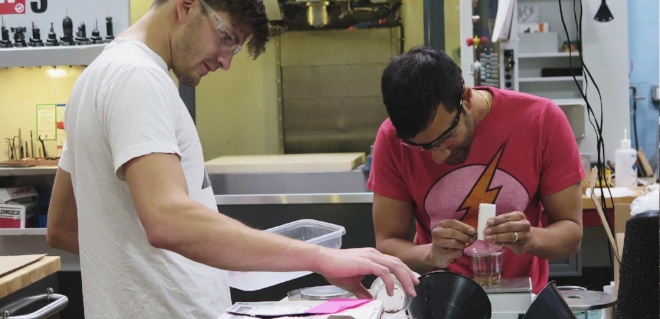
Because the grains were impossible to count individually we would weight them after having determined an average seed/oz count.
The second major challenge was mud. Because Ethiopian soil has up to a 60% clay content, and they plant during the rainy season, it makes for some pretty nasty mud. We had to design a wheel system that would shed mud, or the device would quickly become stuck.
We created a mud test track in an un-used planter behind our offices in Palo Alto. There we did our best to simulate the Ethiopian mud so that we could test different wheel solutions.
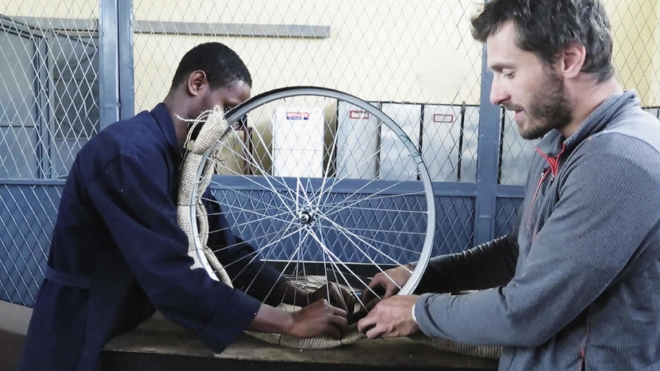
As is often the case, the solution that ended up working the best was one that came directly from the farmers. During the first of three visits to Ethiopia, we learned that they used burlap to cover their cart wheels during the rainy season to prevent mud build up. It was a testament to the power of user interviews and human centered design.
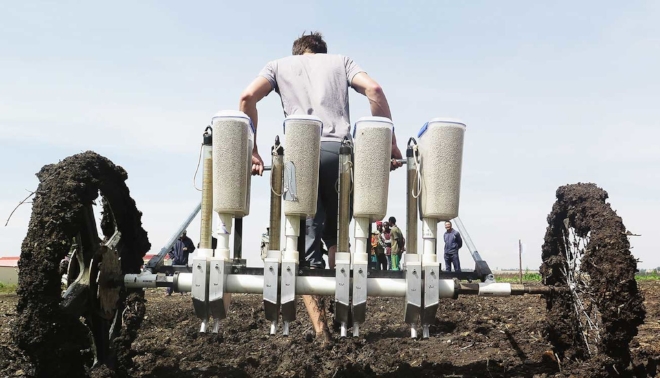
We took our seed and fertilizer dispenser, combined it with our wheel solution and created a simple, human-pulled device. As it’s pulled along the rows, the wheels spin the central square shaft. That shaft in turn spins the metering wheels which dispense the seeds and the fertilizer pebbles in nice even rows. We built a single combined prototype and headed back to Ethiopia for testing.
We returned from our 2-week trip having learned what worked and what didn’t, and set about completely redesigning the planter. A major change was wheels with no spokes to prevent mud clumping. Seen here is one of the wheels made using vacuum forming with hooks for the burlap, and a ratchet system to prevent backdriving. We also added a simple disengagement tab to allow farmers to move the planter without dispensing seeds.
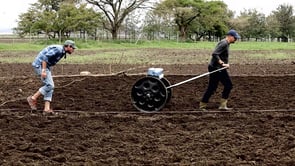
Using our new wheels, and the injection molded dispensers, as well as new easier to fill hoppers for the seeds and fertilizer, we made 50 of the new planters and shipped them over to Ethiopia for trials.
I had left IDEO when this movie was put together, but Aaron Peck and I did all of the final design for the pilot run of 50 machines.
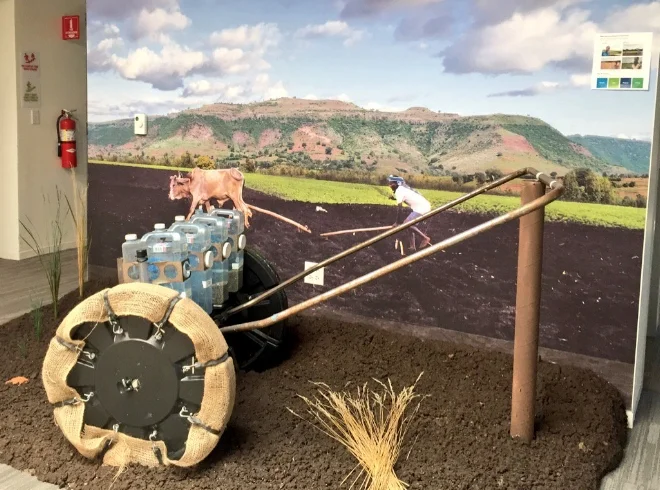
The design was further refined by Northwestern students who continued the project as part of their design program. Seen here is the latest model, with a better set of wheels, but largely unchanged.