Ford Greenfield Labs - Pelikan
Ford’s Greenfield Labs is tasked with exploring new and interesting business models and offerings to help keep Ford at the top of the automotive industry worldwide.
www.GreenfieldLabs.com
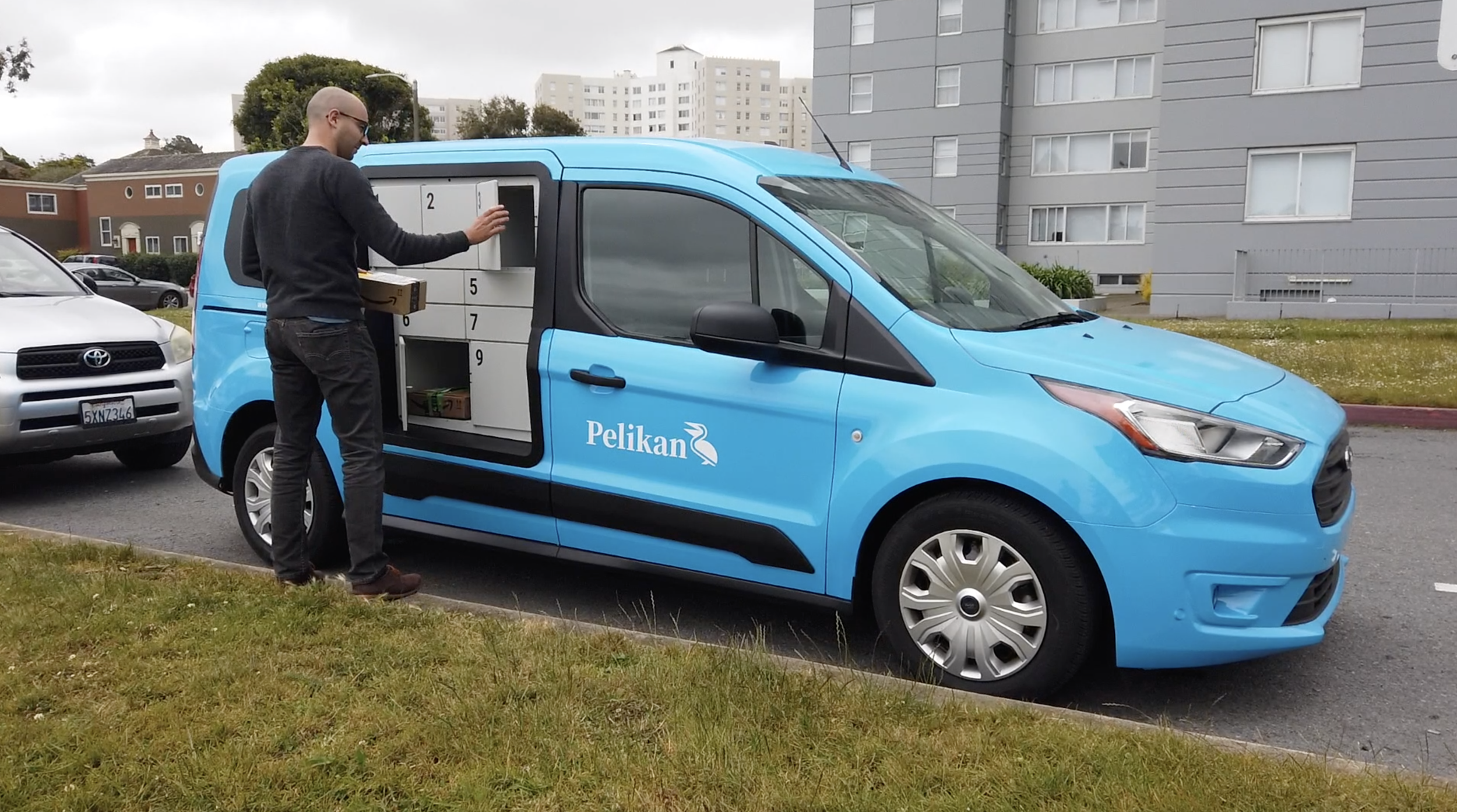
I was engaged to build 2 working prototypes for a pilot project investigating different package delivery modes in the span of 12 weeks.
The first vehicle was equipped with two banks of lockers to investigate a mobile version of Amazon Locker. The door latches were automatically activated using a QR code from the recipients phone.
The second van had larger compartments targeted at curbside delivery. The doors would open automatically using powered cabinet hardware by activating the same QR code system.
The vans started life as empty shells which we promptly cut holes in.
To make the prototypes feel polished, I designed a bezel used the car CAD to match the contours of the van. The bezels were the same across both vans.
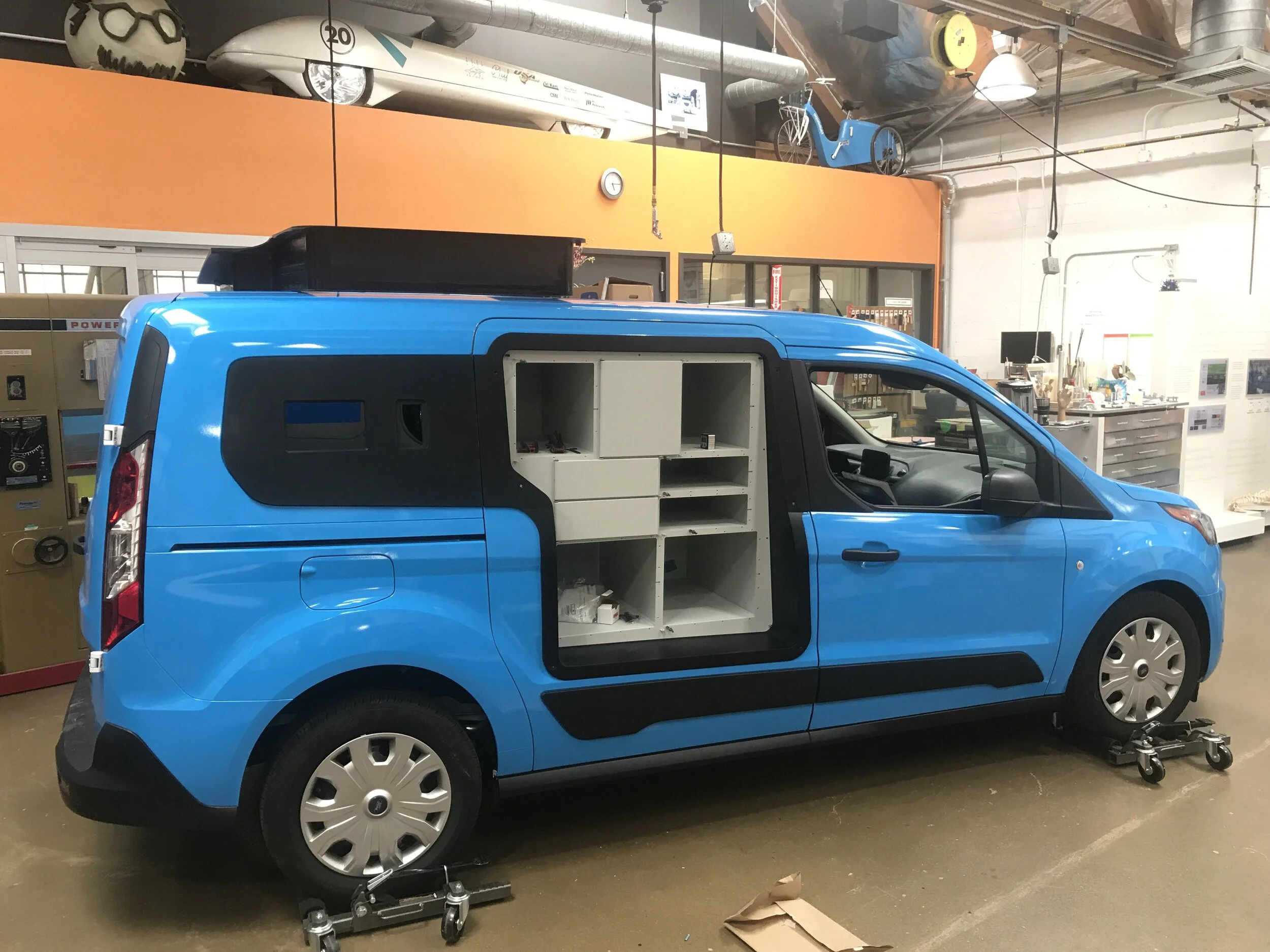
The locker and curbside compartments where powder coated sheet metal assemblies that were put together outside the van, then slid into place through the bezel.
Welded frames inside the van supported the cabinet assemblies and were bolted to the frame of the van. The lights, latches and motors were controlled by Raspberry Pi system with a custom breakout board designed by the Ford Rapid Prototyping team. The whole system ran off a mobile battery to ensure it would not drain the van’s starter battery.


I also worked with the Ford prototyping team to spec a touch screen and camera system to create a kiosk style interaction point for the user.